Induction hardening
Induction hardening is a hardening process in which the surface layer can be partially hardened by a local electric heating to austenitizing temperature via electromagnetic fields, by means of inductors and faster cooling down with water, up to a defined depth.
The induction process is easy to control by electric variables. Distortion is low. Compared to flame-hardening, there is a homogeneous hardness structure in terms of quality.
Optimum hardening results are achieved for heat-treatable steels with a carbon content of more than 0.3 %, e. g., Ck 45 or 42 CrMo4V.
Our CNC plant designed as a tandem version enables us to simultaneously harden two components per work step (max. weight 25 kg, max. length 700 mm).
If desired, a hardness development curve can be prepared after the hardening process, possibly followed by a crack-surface inspection (“fluxing”).
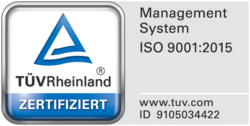