Plasma nitriding - Plasma nitrocarburizing
The plasma nitriding and plasma nitrocarburizing processes are thermochemical diffusion processes which stand out due to their process quality and their ecological safety. Nitriding means that the surface layer of a workpiece is enriched with nitrogen. An additional diffusion of carbon is called nitrocarburizing.
Improvements of the tribological properties:
- increase of the wear resistance
- increase of the strength characteristics with alternating stress
- increase of the corrosion resistance.
In case of dimensions defined in advance, both processes can be applied as finish treatments. An expensive grinding process - as for instance with case hardening - can be left out in most cases.
Compared to the alternative salt bath and gas processes, there are further technological advantages for the user providing an increase of the workpiece functions regarding
- compactness of the compound layers
- variation of the layer composition
- partial treatment of component surfaces
- closer tolerances with lower distortion
- Lower roughness (see picture).
In our state-of-the-art pulse-plasma nitrocarburizing plants, workpieces with a diameter of up to Ø 900 mm and a length of up to 2000 mm can be treated with a maximum individual weight of up to1 t.
Nitriding hardness depths of 0.1 to 1 mm can be reached. All Fe-C compounds, forged or cast, can be treated; the layer hardness depends on the respective alloy constituents.
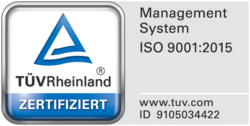